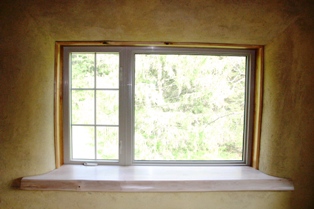
Maple sills and cherry window trim |
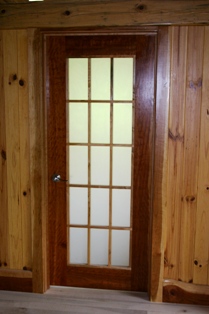
Cherry and glass interior doors |
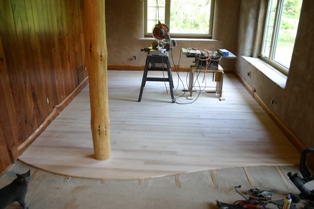
Urban harvested silver maple dinning floor |
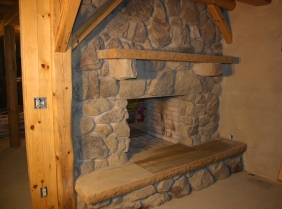
Master bedroom sandstone hearth/mantel |
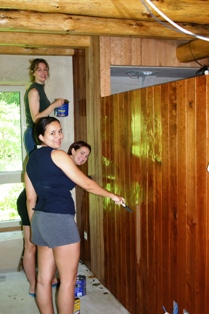
Diana, Robyn, Caryn apply low-VOC tung oil and clear finish |

Ohio sandstone window seats, fireplace hearth and mantels |
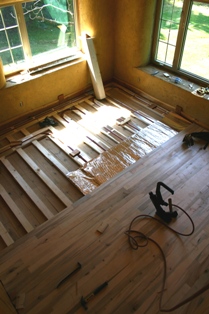
2nd floor sleepers, radiant heat tubing, reflective aluminum and maple hardwood |
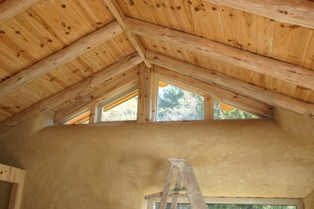
Peak windows east BDR |
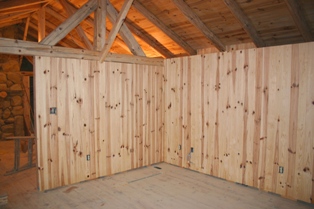
Red pine walls East BDR |
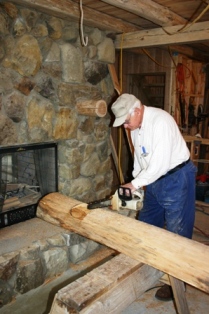
Walt carves custom mantels |
.JPG)
Cherry T&G walls in MBR |
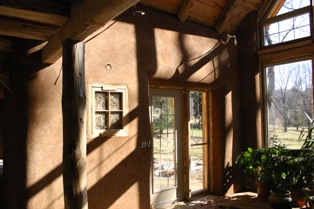
Truth window one step closer to completion |
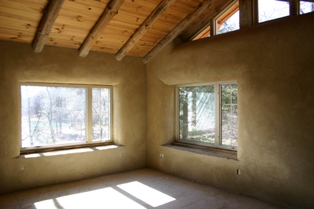
Finished interior plaster curves...what straw bale is all about |
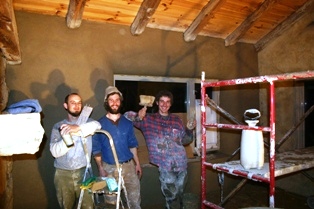
Finish plaster crew with master plasterer, Chris Fox |
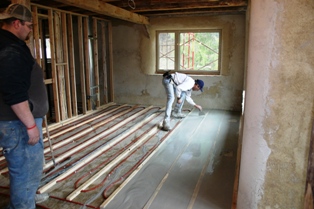
Radiant floor heat and gypcrete thermal mass |
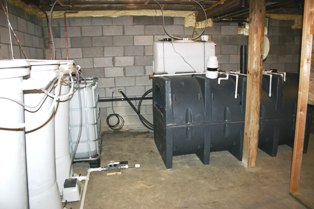
Whole house toilet composting and grey water treatment |
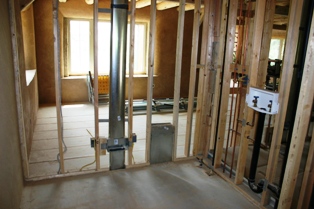
Traditional stud interior walls, electric and plumbing |
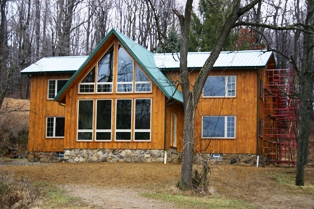
Ecofriendly stain |
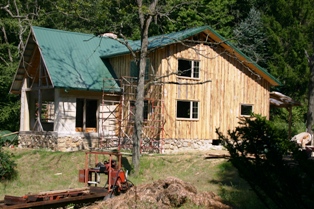
Roughsawn red pine vented rainshield (siding) and windows |
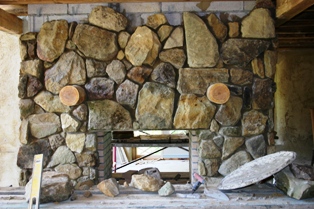
Fireplace with local sandstone facing |
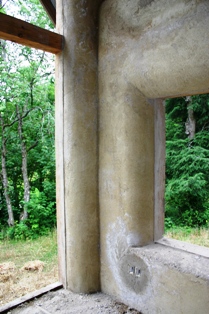
Rough plaster over lath curves and around electric outlets |
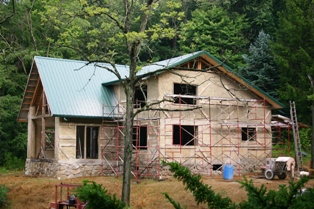
Rough plaster applied inside and out to completely encase bales |
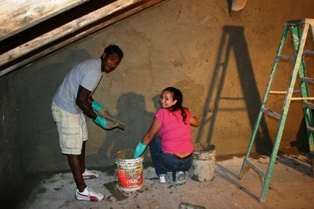
Hand trowel rough plaster coat to create flats and curves |
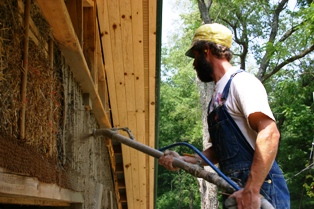
Custom stucco pump applies earthen plaster to bales |
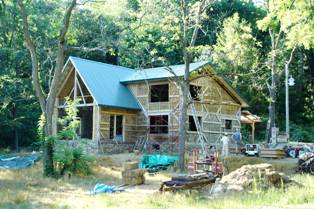
Slip coat of clay over bales to improve plaster adhesion |
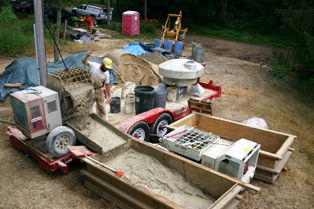
Mix 15 tons of earthen plaster |
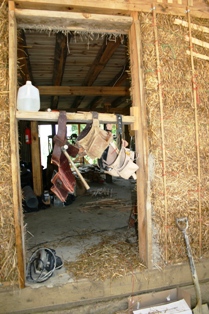
Hang up the tools on the hitching post...time to plaster |
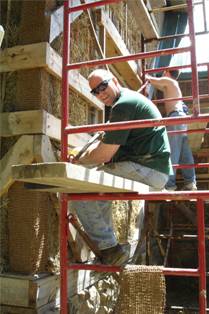
Cover wood with coconut netting to make plaster stick |
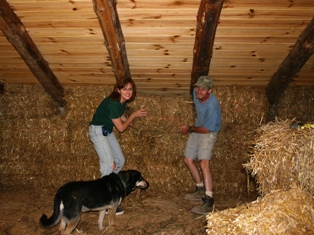
Diana and Paul put in the last of 350+ bales |
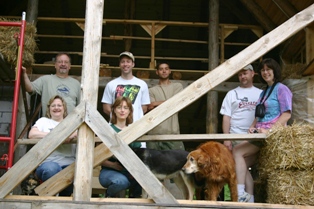
More bale crew volunteers |
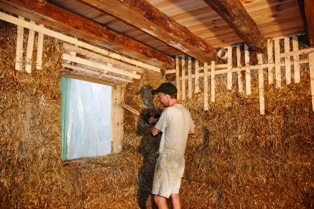
Hedge trimmers make walls flat and curves consistent |

Stuff straw clay into forms and gaps between bales |
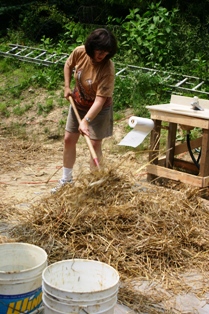
Toss loose straw and hydrated clay for stuffing lath forms |
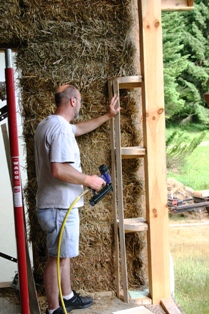
Use form and lath to create custom curves |
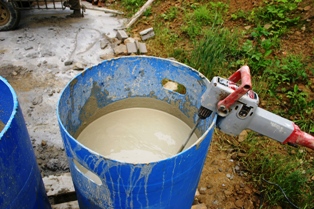
Hydrate clay to milkshake consistency |
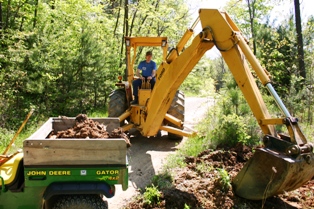
Harvest clay for straw clay and finished plaster mixtures |
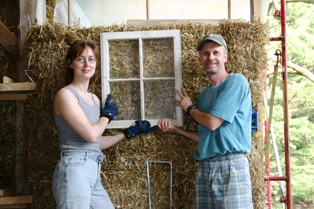
Truth window from original cabin to show straw walls |
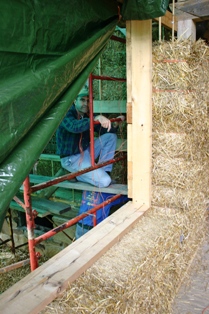
Threat of rain? Work under tarps. |
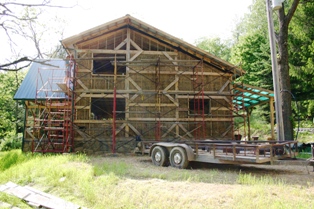
East wall with bales in place |
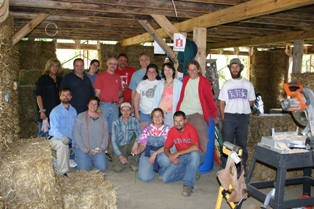
Some of the bale crew |
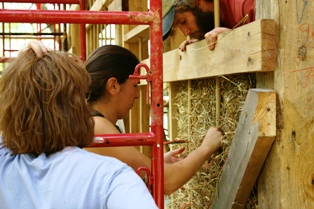
Bale needles used to tie both bale strings to bamboo |
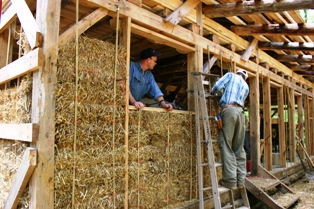
Stack bales like bricks against bamboo |
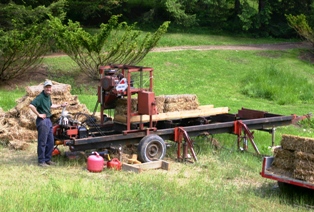
Narrow or angled bales custom cut on bandsaw mill |
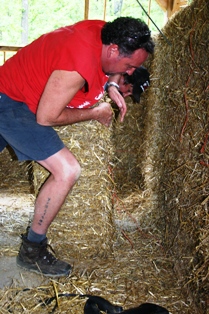
Bales retied to create "short bales" |
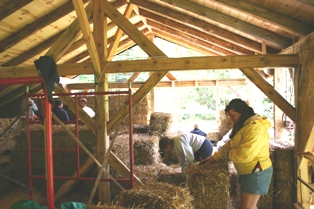
Bales are squared with knife to fit more like bricks |
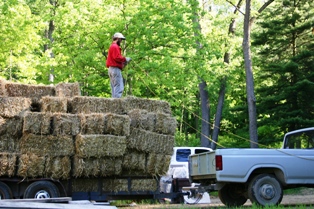
H'ya lil doggy and get those bales to that crazy house |
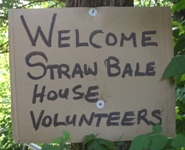
Recruit over 60 family, friends and like-minded volunteers to help |
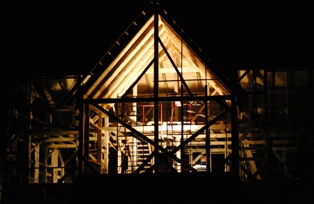
Twas the night before bales and all through the house... |
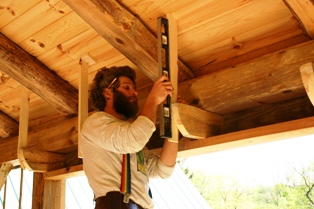
Window curves created with forms and lath |
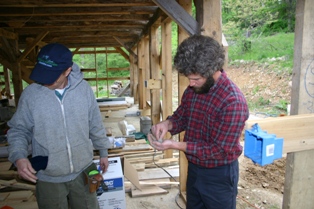
Exterior wall wiring goes in and "experts" prepare for bale work |
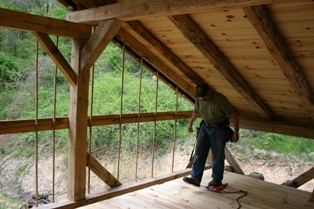
Bamboo reinforcing for tying-off straw bale walls |
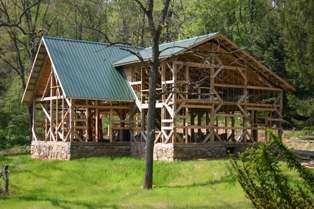
Horizontal nailers for roughsawn vertical siding |
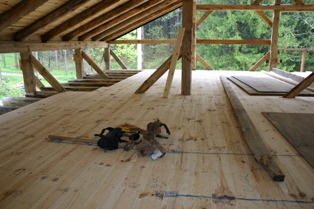
Red pine subfloor (exposed as first floor ceiling) |
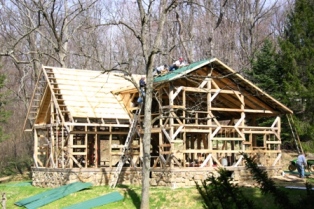
Locally manufactured steel roof |
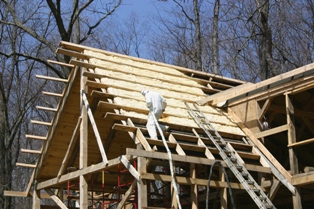
R35, soybean-based, no VOC, BioFoam insulation |
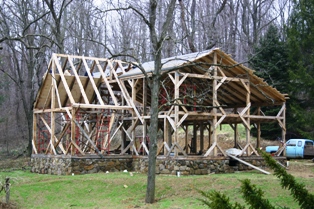
Locally milled red pine roof deck (exposed as ceilings) |
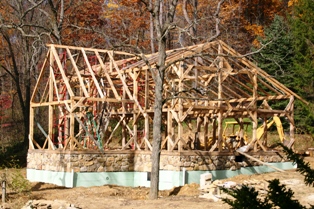
Saltbox and vaulted roof lines |
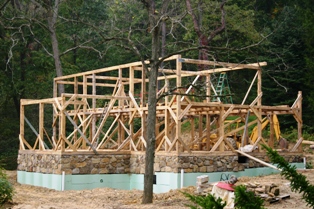
Second floor timber frame |
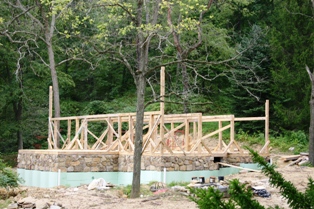
First floor timber frame |
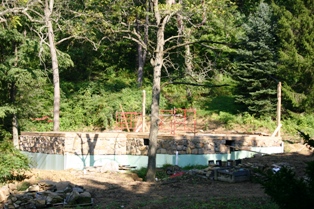
First floor deck on timber joists |
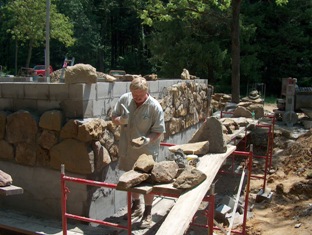
4-6" sand stone facing applied above grade |
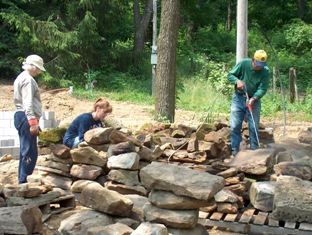
Pressure wash local sandstones for foundation facing |
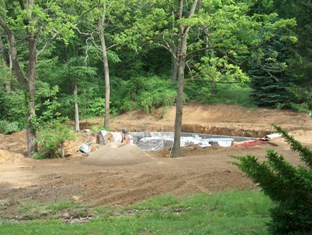
12" block foundation with reinforced cores |
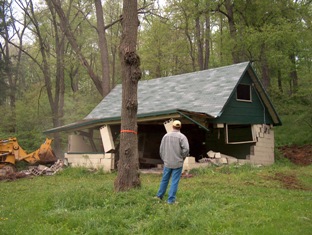
Demolition of last original cabin...argh! |
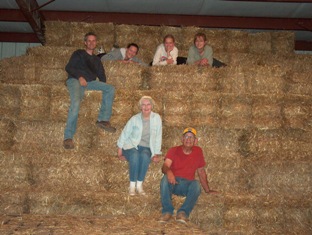
400 bales from Miller farm stored in barn |
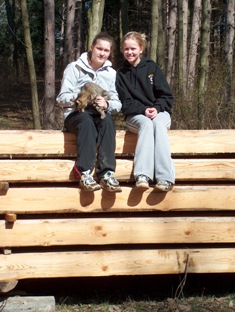
Dry cut timbers |

Use off cuts for exterior vertical siding |
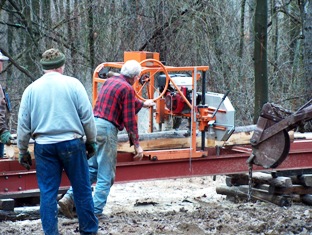
Use portable band mill to saw timbers and dimensional lumber |
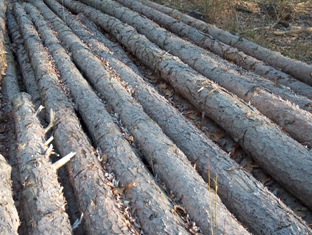
Air dry logs before sawing |
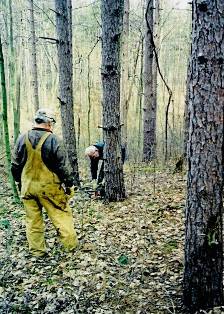
Cut non-native red pine logs from our property |